The Science Behind Porosity: A Comprehensive Guide for Welders and Fabricators
Comprehending the elaborate mechanisms behind porosity in welding is vital for welders and fabricators making every effort for impressive workmanship. As metalworkers explore the depths of this phenomenon, they uncover a world controlled by numerous aspects that influence the formation of these minuscule spaces within welds. From the make-up of the base materials to the details of the welding process itself, a wide variety of variables conspire to either exacerbate or minimize the visibility of porosity. In this comprehensive overview, we will untangle the scientific research behind porosity, discovering its impacts on weld quality and introduction advanced methods for its control. Join us on this journey with the microcosm of welding flaws, where accuracy meets understanding in the search of perfect welds.
Recognizing Porosity in Welding
FIRST SENTENCE:
Exam of porosity in welding discloses crucial insights into the integrity and quality of the weld joint. Porosity, identified by the visibility of dental caries or spaces within the weld steel, is an usual concern in welding processes. These gaps, otherwise correctly dealt with, can compromise the architectural honesty and mechanical buildings of the weld, causing prospective failures in the completed product.

To spot and quantify porosity, non-destructive testing approaches such as ultrasonic screening or X-ray examination are typically used. These strategies permit for the recognition of internal problems without compromising the integrity of the weld. By assessing the dimension, shape, and distribution of porosity within a weld, welders can make informed decisions to improve their welding procedures and achieve sounder weld joints.

Aspects Influencing Porosity Formation
The occurrence of porosity in welding is influenced by a myriad of factors, ranging from gas protecting performance to the details of welding parameter setups. Welding parameters, including voltage, current, travel rate, and electrode type, likewise impact porosity development. The welding strategy employed, such as gas steel arc welding (GMAW) or protected steel arc welding (SMAW), can influence porosity formation due to variants in warm distribution and gas coverage - What is Porosity.
Results of Porosity on Weld Quality
Porosity development dramatically jeopardizes the architectural honesty and mechanical homes of welded joints. When porosity is existing in a weld, it creates voids or tooth cavities within the product, reducing the general toughness of the joint. These gaps act as tension focus points, making the weld more prone to breaking and failure under lots. The existence of porosity also damages the weld's resistance to deterioration, as the trapped air or gases within the gaps can respond with the surrounding environment, resulting in degradation gradually. Additionally, porosity can hinder the weld's capability to hold up against stress or effect, additional jeopardizing the general high quality and integrity of the bonded structure. In essential applications such as aerospace, automotive, or structural building and constructions, where safety and security and why not try this out toughness are vital, the harmful results of porosity on weld high quality can have severe consequences, emphasizing the significance of minimizing porosity with correct welding strategies and treatments.
Methods to Decrease Porosity
Furthermore, utilizing the suitable welding specifications, such as the proper voltage, current, and take a trip speed, is important in protecting against porosity. Preserving a consistent arc length and angle during welding likewise assists reduce the likelihood of porosity.

Utilizing the appropriate welding strategy, such as back-stepping or utilizing a weaving movement, can also assist distribute warmth equally and reduce the possibilities of porosity development. By go to this website executing these strategies, welders can properly minimize porosity and generate high-grade bonded joints.
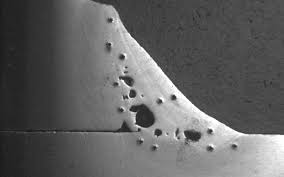
Advanced Solutions for Porosity Control
Applying innovative modern technologies and ingenious techniques plays a pivotal duty in accomplishing exceptional control over porosity in welding procedures. Additionally, utilizing advanced welding techniques such as pulsed MIG welding or customized ambience welding can likewise help mitigate porosity problems.
An additional sophisticated option includes the use of sophisticated welding devices. Using devices with integrated attributes like waveform control and innovative power sources can enhance weld quality and decrease porosity dangers. The application of automated welding systems with exact control over specifications can dramatically decrease porosity issues.
In addition, including innovative surveillance and examination modern technologies such as real-time X-ray imaging or automated ultrasonic screening can assist in identifying porosity early in the welding procedure, enabling prompt rehabilitative activities. In general, incorporating these innovative options can considerably enhance porosity control and enhance the general quality of welded elements.
Final Thought
In conclusion, recognizing find out here the scientific research behind porosity in welding is vital for welders and fabricators to generate high-grade welds. By determining the elements influencing porosity development and carrying out techniques to lessen it, welders can enhance the total weld top quality. Advanced services for porosity control can better enhance the welding procedure and guarantee a strong and trustworthy weld. It is essential for welders to continuously inform themselves on porosity and execute finest practices to attain optimal outcomes.